In maritime container shipping, multiple parties handle cargo, creating unique challenges around communication and accountability. This post explores common causes of cargo damage and practical tips for minimizing risks, from proper container stuffing to advanced tracking solutions.
Common causes
In overseas maritime container shipping, there are many different parties involved. A great advantage of this practice is that it has allowed companies to specialize in different phases of the logistics process, greatly reducing costs, increasing both efficiency and geographical outreach. On the other side, having so many stakeholders responsible for one shipment can make communication difficult and responsibilities or liability unclear.
On a typical international full container shipping route, below are the parties that may physically handle cargo:
- The supplier/factory loading the cargo.
- The local trucker delivering the cargo to a local warehouse.
- The local dray company moving the cargo from the warehouse to the terminal
- The origin terminal
- The transshipment terminal
- The arrival port terminal
- Customs or the customs warehouse (if there is any customs hold)
- The local trucker at the arrival port for final delivery
Explore Dockflow’s Container Visibility Solution
The container is physically handled at all of these locations, by all these different parties.
During an ocean voyage, ships very often encounter turbulent waters. Cargo that is not properly secured will unavoidably shift. The most common reasons for cargo damage are water damage, impacts that the container took, and damages due to improper lashing and stuffing.
Water damage
Did you know that 1 in 5 cargo damages are the result of water damage? Water damage may occur due to different reasons:
- Condensation inside a container, especially if the container is being stuffed at high humidity temperatures.
- Temperature changes during the voyage of the vessel may also increase the condensation inside the container, which may cause the cargo to get wet.
- Water may get inside the container if there are any small holes in it, especially during the voyage if a vessel encounters poor weather conditions.
Improper stuffing and lashing
Proper container stuffing should not be taken lightly. Shifting cargo and uneven weight distribution are some of the most common causes of cargo damage, in addition to bad packaging, choosing inadequate containers, improper loading of the pallets and poor labeling.
Prevention
The science of stuffing
The UK P&I club claims over half of cargo damage cases could be avoided through more careful stuffing. A minimal amount of time could save you a lot of expense in the long run.
Shippers or other stakeholders involved with loading the containers must be educated on the below details:
- The space utilization must be carefully checked for palletized cargo, and if there are any empty spaces between pallets, they need to be filled with airbags or other means of fillers.
- The distribution of the weight inside the container needs to be even.
- Loading heavier items on the side or at one end of the container must be avoided.
- Stow the lighter items on top of the heavier items and avoid stuffing any loose item, and pack the cargo as tight as possible.
Choosing the Right Container
Containers come in several types, lengths, widths and heights. Match this to your requirements. Do not pick a container that when loaded exceeds the size or weight limit at any stage of the journey.
Do not overlook climatic changes along the route that could affect your cargo. Choose a container type that is appropriate. It is often a false economy to avoid the additional cost of a container with a fan, temperature control or ventilation. Temperatures can increase inside a container e.g. a tropical climate can produce temperatures of 50 degrees plus which in turn causes condensation and roasting.

Finally, make sure the container has enough lashing points of the strength you require. Confirm your requirements in writing to the container operator and draw on the experience of the container operator. Remember the responsibility of choosing equipment is not down to the container operator. The liability is on you!
Checking Your Container
For peace of mind take a few minutes to check over the container. Be wary of residues – they could be hazardous or contaminate your consignment. If in any doubt return the container for cleaning. Watch out for structural damage such as damage to post rails or corner castings. This can cause damage to cargo. Check that you can securely lock the doors. If in doubt: reject the container!
Always check that the container is dry. Are there any holes made by handling equipment that could let in moisture? Ensure that the gaskets aren’t hard, damaged or worn. Look out for stains around the door area as this can indicate a previous leak. Check for rust (rust is porous). Do a light test that can reveal small holes in the container.
Finally, be on the lookout for taped up vents and old labels as these can be misleading and lead to delays.
Take delivery of your container with care
Just a few minutes of your time can reduce the chance of your cargo being damaged. If you overlook defects which a court decides due diligence would have revealed, you may find an insurance claim is drastically reduced or even rejected.
Have a solid Packing Plan
Most operators charge by the container load. The more goods you can fit into the container, the lower the unit price will be to ship your goods. It is wise to draw up a packing plan to maximize the fill factor. Remember: less free space in the container means less risk of cargo shifting. If cargo doesn’t fill the container, start by covering the floor space at an even height. If you have to leave gaps, try and leave them in the center so that the cargo can be secured by wedging them to the side walls.
Weight must be evenly spread; side to side, end to end. Always keep the center of gravity as low as possible. Never exceed the container’s maximum payload or exceed any of the weight restrictions on route.
If the upper tier doesn’t run the full length of the container a vertical separator can be used to restrain it. If suitable use an interlocking stow. Unitized cargo is often more stable and quicker to pack. Make a point of strongly shoring and blocking the face of the stow as this prevents the cargo from falling out when the doors are open.
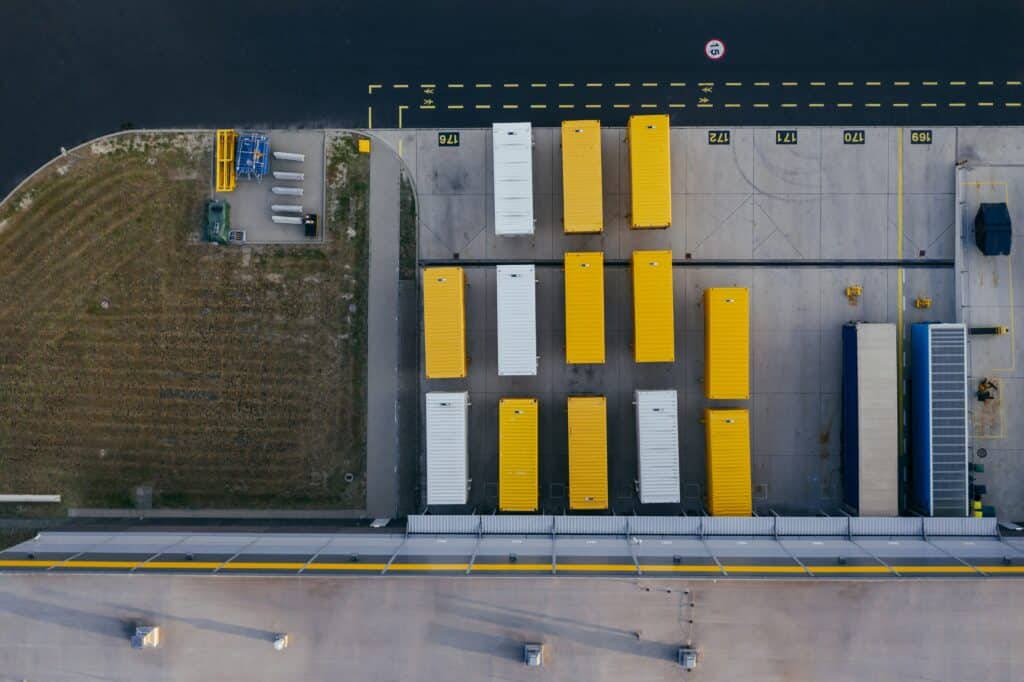
Place the heaviest items in the center of the container. Place large heavy items on the bottom of the container and lighter ones on the top. Always place liquids underneath dry goods. Ensure drums and barrels are stowed with the bung upwards and if possible separated as vibration can wear away the seams and allow the contents to escape. It is best to use a double layer of dunnage to limit damage.
Ensure you are aware of the safe loading limits of the lashing points. Do not pack cargoes that are incompatible together e.g. cargoes that are prone to sweating packed with moisture sensitive cargo.
Know the specific documentation and inspection requirements
Goods that are subject to Pre-Shipment Inspection (PSI) should be stored at the door end. Some destination countries want a packing list fixed to the inside of the container door. Some destination countries require wood treatment certificates attached here too. Declare the cargo weight accurately.
Cargo shifting and weight distribution
Shifting cargo and uneven weight distribution are some of the most common causes of cargo damage. The forces exerted on a container’s contents in transit by road, rail, ship or gantry crane are considerable. If the contents are not properly secure, no matter how heavy, damage will occur. Many shippers tend to undercut costs by not packaging their goods properly which often leads to crushed, unsalable goods. Appropriate packaging should be used to protect your investment.
Remember: free space in a container increases the risk of cargo shifting. Packaging that fits in exactly (i.e. cardboard boxes) will reduce dead space and reduce the cost of dunnage. All loose items must be chocked/lashed.
Stretch or shrink wrap is great for protection against wet damage. It’s not cheap but could save you money in the long run. Use dunnage to protect non-unitized cargoes from damage.
Dunnage
Dunnage: Materials of various types, often timber or matting, placed among the cargo for separation, and hence protection from damage, for ventilation and, in the case of certain cargoes, to provide a space in which the tines of a forklift truck may be inserted.
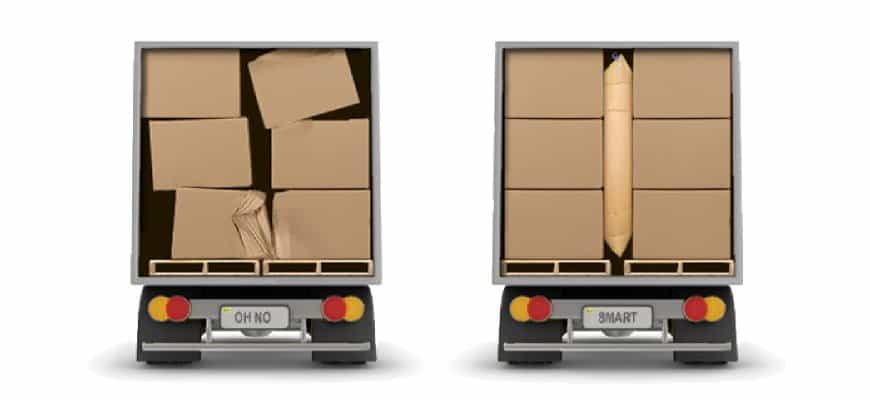
Ensure that dunnage is not wet or made from unseasoned wood as this may cause condensation and damage. Be careful to check the quarantine regulations in the port of destination as they may require the dunnage to be treated or fumigated.
Airbags are a modern method which is easier to use than conventional shoring. Remember not to place them where they can force open the doors!
Security
No seal can stop a thief. Its main function is to signal where and when a container has been broken into. Bolt seals are the best. Always check the seal and ensure it is the right type. Tug the seal to ensure that it is properly locked.
Always record the date and the seal number and keep these records safe. Enter the seal number on all shipping documentation and lock the papers somewhere safe. Never leave the sealing of a container to a third party. Who knows how honest they are?
Finally, arrange a convenient time for your cargo to be delivered as this reduces the time the container is exposed to the elements and the risk of theft.
Safety and Unpacking
Do not overlook what type of equipment the consignee has for unloading the container. Always look at all external notices/labels before you open the container. If the contents are hazardous and appears to be leaking you should evacuate the area immediately. If the container is exceptionally hot move it to a safe place and call the fire service. If gas is present let it dissipate before entering the container.
Always document the external appearance of the container. Are there any dents, holes, rust…. Inspect the internal contents of the container for damage and document any found. It is always best to take photographs where possible as this could assist any claims.
Always check the seal is the right type and that the serial number agrees with the documentation. Has the seal been tampered with? Always keep both parts of the seal until you have checked that all the cargo is present and correct.
Safety goggles and overalls should be worn. A useful idea is to use a strap tied around the door stanchions. This will prevent the doors from swinging open and goods falling on you. Once you know you are safe you can remove the strap and open the container fully.
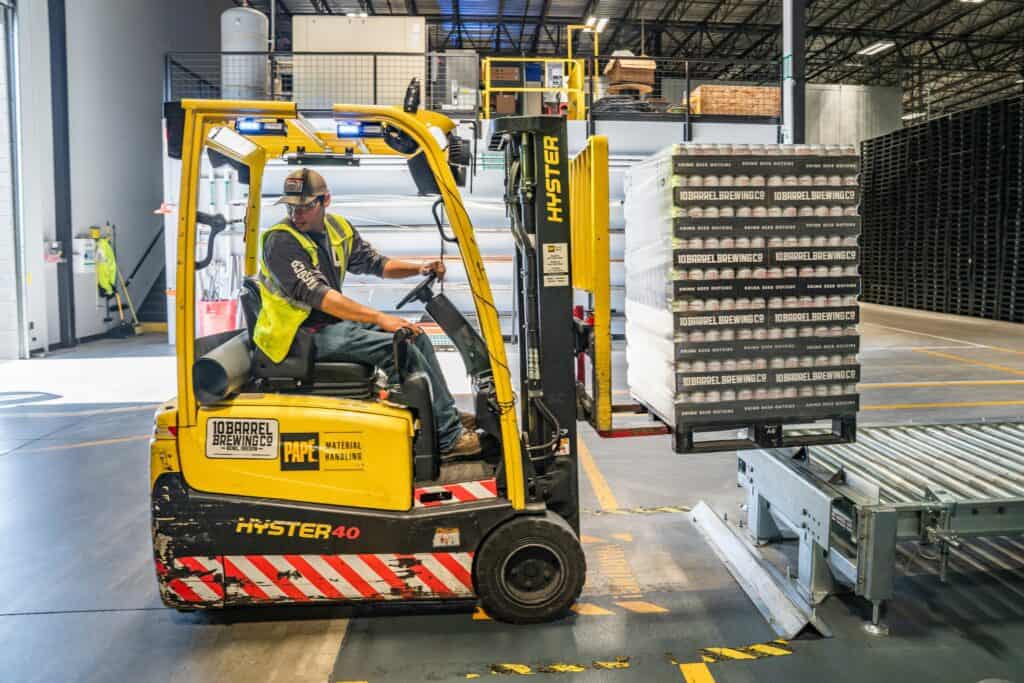
Once opened, doors can easily cause damage if the wind slams them – secure them open. It is the consignee’s responsibility to clean the container to a level that you would wish to receive it.
Responsibilities of the shipping line
Officers are always on deck supervising local stevedores who are not familiar with the vessels. Lifting and lashing equipment is regularly examined to ensure that it is in good working order, to manufacturers guidelines. All damaged equipment is removed immediately. Spares are always carried on board.
A stowage planner is only as good as the data he receives. The shipping line ensures that stack and weight limits and complete stowage position plans are made available for the crew. This is necessary to verify that container racking limits are not exceeded, hatch covers and tank tops are not overstressed and stows are safe and secure. Staff routinely monitor the stow throughout the voyage.
A thorough examination of all stowage methods is done prior to sailing. This includes checking twist locks, galvanized rods, securing points, and base sockets.
Dangerous goods are segregated as per the IMDG code, national legislation and the ship’s dangerous goods document of compliance. Hazardous goods are always checked once loaded to ensure it is safely stowed and there are no leaks.
Reefer containers are stowed only where they can be connected to electrical power supplies. All reefers are set to the temperatures as specified by the shipper and staff make routinely checks throughout the voyage. Non-containerized cargo is given a protective stow.
Stack weight limits should never be exceeded. Heavy containers are stowed in tiers so that late arrivals which are heavy do not end up on deck or on top of the stack.
In case of damage
When the container is received at the warehouse, a thorough inspection is needed. Check if there is any visible damage to the container from outside. Once the unloading starts, if there is any visible damage to the cargo, stop the unloading process immediately and notify your carrier and your insurance company, if the cargo is insured. If there is extensive damage reported, your carrier might decide to send a surveyor to jointly unload the cargo.
In order to claim the damage from your carrier, you will need to send the following documents to the carrier:
- First Notice of Intent to Claim
- Survey Report
- Photos
- Shipper’s Commercial Invoice
- Detailed Claim Statement (the calculation of the loss, based on the commercial value of the cargo)
- Packing List
- Delivery Receipt
- Container Destuffing Tally Sheet
- Proof of Salvage Value/Independent Destruction Certificate (to prove the cargo is indeed damaged and can be sold on a secondhand market.)
The carrier will review the claim and will determine at which point along the journey the damage might have occurred. If the damage occurs when the cargo is under the responsibility of the ocean carrier, they will determine a claim amount and send a claim settlement letter to finalize the claim.
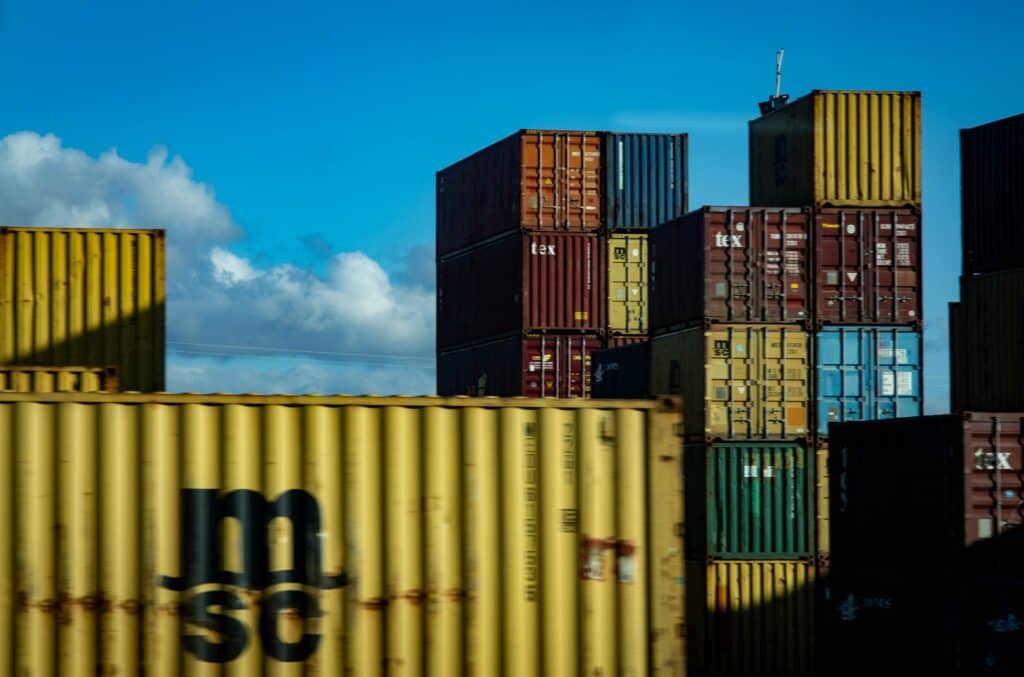
However, if it is determined that damage may have occurred due to other reasons, such as improper stuffing, then they would deny it if they are not the party that stuffed the container. In this case, you will need to file the claim with other parties.
On average, it takes about 3 to 6 months to finalize a damaged cargo claim.
Protecting yourself from the risks of cargo damage
As a forwarder or shipper, there are definitely some steps you can take to reduce the risk of damaged cargo. The basic measures are obtaining cargo insurance, following basic stuffing rules and working with reliable carriers. For more advanced insights and live alerts for high-value or condition-sensitive cargo (chemicals, perishables, electronics, …) consider using IoT devices connected to a smart platform such as Dockflow
Free download: 10 tools to prevent cargo damage losses
Modern IoT solutions and intelligent algorithms allow you to protect your cargo and provide transparency in case of damage claims. Download our free guide on how to prevent cargo damage losses through IoT, AI and blockchain:
Sources
Six tips for reducing cargo damage in the shipping process
https://www.agcs.allianz.com/news-and-insights/news/safety-shipping-review-2019.html
https://www.morethanshipping.com/what-is-damaged-cargo-and-how-to-prevent-and-handle-it